



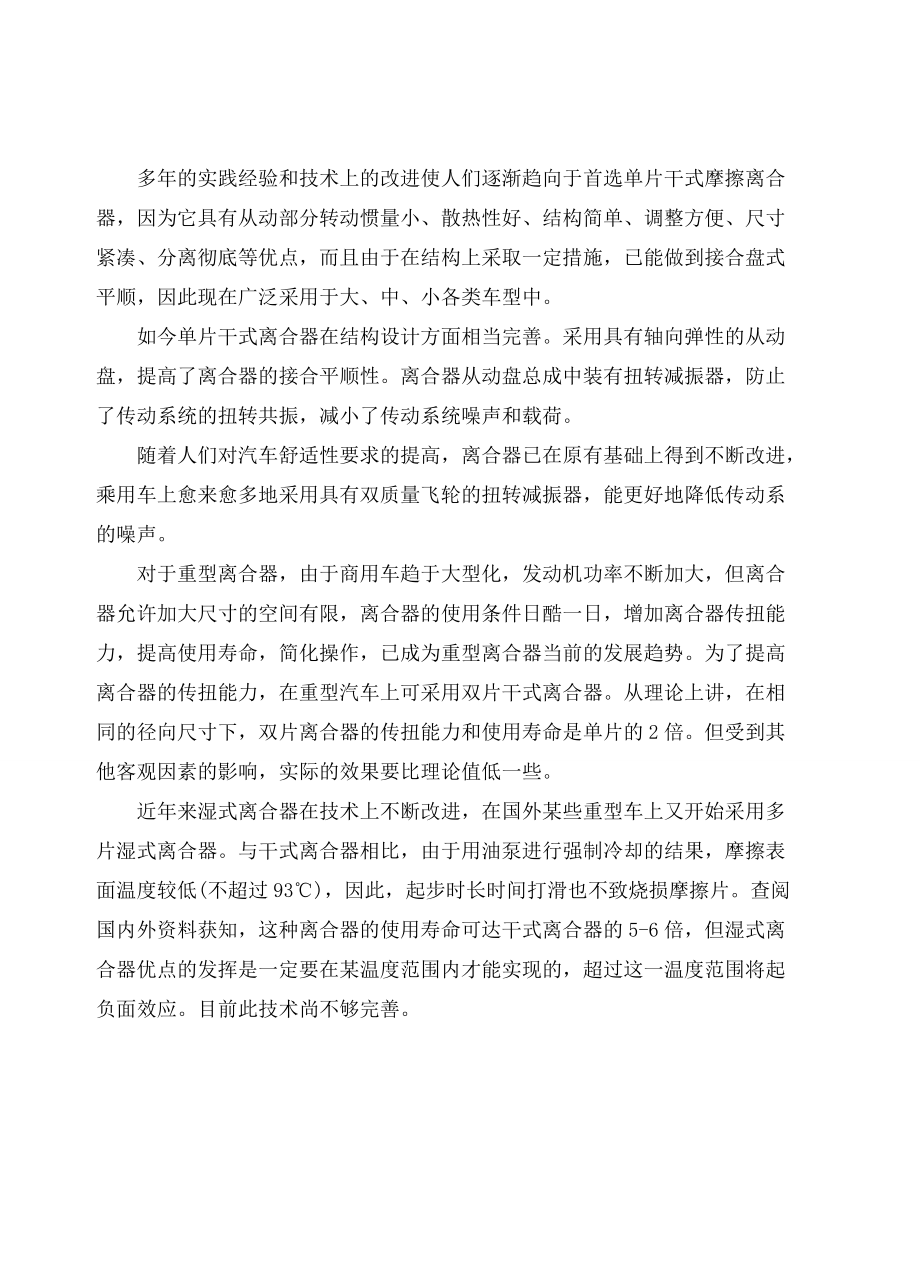
版權說明:本文檔由用戶提供并上傳,收益歸屬內容提供方,若內容存在侵權,請進行舉報或認領
文檔簡介
1、GDGM-QR-03-077-B/1畢業綜合實踐報告題目:離合器畢業設計論文系 別: 汽車電子技術 班 級: 13汽電1班 學生姓名: 陳政宇 學 號: 1322134 指導老師: 郇瑞鐵 完成日期: 汽車離合器畢業設計論文摘 要本設計主要分析了膜片彈簧離合器,對膜片彈簧離合器進行了分類,闡述了膜片彈簧離合器的原理和組成,及其特性。通過詳細的推導過程積累了大量的數據,并成功的繪制出了膜片彈簧離合器的成品圖。敘述了離合器的發展現狀,和它的工作原理,在此過程中,經過對比結合,初步確定了合適的離合器結構形式,選取了拉式膜片彈簧離合器,并且帶有扭轉減振器,為后面的計算提供了理論基礎。在計算中,首先確定
2、摩擦片外徑尺寸,然后根據該尺寸對其他部件總成進行了計算和設計。通過計算校核摩擦片外徑尺寸,計算選擇出其他部件的外形尺寸,再對其進行校核,確定是否能達到設計要求。設計包括對從動盤總成的設計校核,對壓盤的設計校核,對離合器蓋的設計校核及離合器蓋的設計校核和優化。具體設計計算了摩擦片、扭轉減振器、膜片彈簧、壓盤、離合器蓋、傳動片等多個部件總成在上述工作完成之后,通過計算機Pro/E軟件的學習運用,對離合器總體裝配圖、從動盤總成、壓盤、膜片彈簧、摩擦片進行了繪制,在繪制的過程中對離合器的裝配又有了進一步的理解,并且完善了計算部分的遺漏。 這次的設計,可以對原有離合器的設計提出優化和修改的建議,對其以后
3、的設計過程起參考作用。通過這次設計達到了優化改進原有離合器,提高該型汽車使用性,舒適性,并提高了汽車的工作效率的目的。1 緒 論1.1引 言以內燃機作為動力的機械傳動汽車中,離合器是作為一個獨立的總成而存在的。離合器通常裝在發動機與變速器之間,其主動部分與發動機飛輪相連,從動部分與變速器相連。為各類型汽車所廣泛采用的摩擦離合器,實際上是一種依靠其主、從動部分間的摩擦來傳遞動力且能分離的機構。離合器的主要功用是切斷和實現發動機與傳動系平順的接合,確保汽車平穩起步;在換擋時將發動機與傳動系分離,減少變速器中換檔齒輪間的沖擊;在工作中受到較大的動載荷時,能限制傳動系所承受的最大轉矩,以防止傳動系個零
4、部件因過載而損壞;有效地降低傳動系中的振動和噪音。1.2離合器的發展在早期研發的離合器結構中,錐形離合器最為成功。它的原型設計曾裝在1889年德國戴姆勒公司生產的鋼制車輪的小汽車上。它是將發動機飛輪的內孔做成錐體作為離合器的主動件。采用錐形離合器的方案一直延續到20世紀20年代中葉,對當時來說,錐形離合器的制造比較簡單,摩擦面容易修復。它的摩擦材料曾用過駱毛帶、皮革帶等。那時曾出現過蹄-鼓式離合器,其結構有利于在離心力作用下使蹄緊貼鼓面。蹄-鼓式離合器用的摩擦元件是木塊、皮革帶等,蹄-鼓式離合器的重量較錐形離合器輕。無論錐形離合器或蹄-鼓式離合器,都容易造成分離不徹底甚至出現主、從動件根本無法
5、分離的自鎖現象。現今所用的盤式離合器的先驅是多片盤式離合器,它是直到1925年以后才出現的。多片離合器最主要的優點是,汽車起步時離合器的接合比較平順,無沖擊。早期的設計中,多片按成對布置設計,一個鋼盤片對著一青銅盤片。采用純粹的金屬的摩擦副,把它們浸在油中工作,能達到更為滿意的性能。浸在油中的盤片式離合器,盤子直徑不能太大,以避免在高速時把油甩掉。此外,油也容易把金屬盤片粘住,不易分離。但畢竟還是優點大于缺點。因為在當時,許多其他離合器還在原創階段,性能很不穩定。石棉基摩擦材料的引入和改進,使得盤片式離合器可以傳遞更大的轉矩,能耐受更高的溫度。此外,由于采用石棉基摩擦材料后可用較小的摩擦面積,
6、因而可以減少摩擦片數,這是由多片離合器向單片離合器轉變的關鍵。20世紀20年代末,直到進入30年代時,只有工程車輛、賽車和大功率的轎車上才使用多片離合器。早期的單片干式離合器由與錐形離合器相似的問題,即離合器接合時不夠平順。但是,由于單片干式離合器結構緊湊,散熱良好,轉動慣量小,所以以內燃機為動力的汽車經常采用它,尤其是成功地開發了價格便宜的沖壓件離合器蓋以后更是如此。實際上早在1920年就出現了單片干式離合器,這和前面提到的發明了石棉基的摩擦面片有關。但在那時相當一段時間內,由于技術設計上的缺陷,造成了單片離合器在接合時不夠平順的問題。第一次世界大戰后初期,單片離合器的從動盤金屬片上是沒有摩
7、擦面片的,摩擦面片是貼附在主動件飛輪和壓盤上的,彈簧布置在中央,通過杠桿放大后作用在壓盤上。后來改用多個直徑較小的彈簧,沿著圓周布置直接壓在壓盤上,成為現今最為通用的螺旋彈簧布置方法。這種布置在設計上帶來了實實在在的好處,使壓盤上的彈簧的工作壓力分布更均勻,并減小了軸向尺寸。多年的實踐經驗和技術上的改進使人們逐漸趨向于首選單片干式摩擦離合器,因為它具有從動部分轉動慣量小、散熱性好、結構簡單、調整方便、尺寸緊湊、分離徹底等優點,而且由于在結構上采取一定措施,已能做到接合盤式平順,因此現在廣泛采用于大、中、小各類車型中。如今單片干式離合器在結構設計方面相當完善。采用具有軸向彈性的從動盤,提高了離合
8、器的接合平順性。離合器從動盤總成中裝有扭轉減振器,防止了傳動系統的扭轉共振,減小了傳動系統噪聲和載荷。隨著人們對汽車舒適性要求的提高,離合器已在原有基礎上得到不斷改進,乘用車上愈來愈多地采用具有雙質量飛輪的扭轉減振器,能更好地降低傳動系的噪聲。對于重型離合器,由于商用車趨于大型化,發動機功率不斷加大,但離合器允許加大尺寸的空間有限,離合器的使用條件日酷一日,增加離合器傳扭能力,提高使用壽命,簡化操作,已成為重型離合器當前的發展趨勢。為了提高離合器的傳扭能力,在重型汽車上可采用雙片干式離合器。從理論上講,在相同的徑向尺寸下,雙片離合器的傳扭能力和使用壽命是單片的2倍。但受到其他客觀因素的影響,實
9、際的效果要比理論值低一些。近年來濕式離合器在技術上不斷改進,在國外某些重型車上又開始采用多片濕式離合器。與干式離合器相比,由于用油泵進行強制冷卻的結果,摩擦表面溫度較低(不超過93),因此,起步時長時間打滑也不致燒損摩擦片。查閱國內外資料獲知,這種離合器的使用壽命可達干式離合器的5-6倍,但濕式離合器優點的發揮是一定要在某溫度范圍內才能實現的,超過這一溫度范圍將起負面效應。目前此技術尚不夠完善。1.3膜片彈簧離合器的結構及其優點1.3.1膜片彈簧離合器的結構膜片彈簧離合總成由膜片彈簧、離合器蓋、壓盤、傳動片和分離軸承總成等部分組成。1、離合器蓋離合器蓋一般為120°或90°
10、旋轉對稱的板殼沖壓結構,通過螺栓與飛輪聯結在一起。離合器蓋是離合器中結構形狀比較復雜的承載構件,壓緊彈簧的壓緊力最終都要由它來承受。2、膜片彈簧膜片彈簧是離合器中重要的壓緊元件,在其內孔圓周表面上開有許多均布的長徑向槽,在槽的根部制成較大的長圓形或矩形窗孔,可以穿過支承鉚釘,這部分稱之為分離指;從窗孔底部至彈簧外圓周的部分形狀像一個無底寬邊碟子,其截面為截圓錐形,稱之為碟簧部分。3、壓盤壓盤的結構一般是環形盤狀鑄件,離合器通過壓盤與發動機緊密相連。壓盤靠近外圓周處有斷續的環狀支承凸臺,最外緣均布有三個或四個傳力凸耳。4、傳動片離合器接合時,飛輪驅動離合器蓋帶動壓盤一起轉動,并通過壓盤與從動盤摩
11、擦片之間的摩擦力使從動盤轉動;在離合器分離時,壓盤相對于離合器蓋作自由軸向移動,使從動盤松開。這些動作均由傳動片完成。傳動片的兩端分別與離合器蓋和壓盤以鉚釘或螺栓聯接,一般采用周向布置。在離合器接合時,離合器蓋通過它來驅動壓盤共同旋轉;在離合器分離時,可利用它的彈性恢復力來牽動壓盤軸向分離并使操縱力減小。5、分離軸承總成分離軸承總成由分離軸承、分離套筒等組成。分離軸承在工作時主要承受軸向分離力,同時還承受在高速旋轉時離心力作用下的徑向力。目前國產的汽車中多使用角接觸推力球軸承,采用全密封結構和高溫鏗基潤滑脂,其端面形狀與分離指舌尖部形狀相配合,舌尖部為平面時采用球形端面,舌尖部為弧形面時采用平
12、端面或凹弧形端面。1.3.2膜片彈簧離合器的工作原理由圖1.1可知,離合器蓋1與發動機飛輪用螺栓緊固在一起,當膜片彈簧3被預加壓緊,離合器處于接合位置時,由于膜片彈簧大端對壓盤5的壓緊力,使得壓盤與從動盤6摩擦片之間產生摩擦力。當離合器蓋總成隨飛輪轉動時(構成離合器主動部分),就通過摩擦片上的摩擦轉矩帶動從動盤總成和變速器一起轉動以傳遞發動機動力(1)接合位置 (2)分離位置1-離合器蓋 2-鉚釘 3-膜片彈簧 4-支撐環 5-壓盤6-摩擦片 7-分離軸承總成 8-離合器踏板 9-輸出軸圖1.1膜片彈簧離合器的工作原理圖要分離離合器時,將離合器踏板8踏下,通過操縱機構,使分離軸承總成7前移推動
13、膜片彈簧分離指,使膜片彈簧呈反錐形變形,其大端離開壓盤,壓盤在傳動片的彈力作用下離開摩擦片,使從動盤總成處于分離位置,切斷了發動機動力的傳遞。1.3.3膜片彈簧離合器的優點膜片彈簧離合器與其他形式離合器相比,具有一系列優點:1、膜片彈簧離合器具有較理想的非線性彈性特性;2、膜片彈簧兼起壓緊彈簧和分離杠桿的作用,結構簡單、緊湊,軸向尺寸小,零件數目少,質量小;3、高速旋轉時,彈簧壓緊力降低很少,性能較穩定;4、膜片彈簧以整個圓周與壓盤接觸,使壓力分布均勻,摩擦片接觸良好,磨損均勻;5、易于實現良好的通風散熱,使用壽命長;6、膜片彈簧中心與離合器中心線重合,平衡性好。1.4設計內容1、壓盤設計。2
14、、離合器蓋設計。3、從動盤總成設計。4、膜片彈簧設計。1.5 Pro/E軟件的特點Pro/Engineer是美國PTC公司開發的一套機械CAD/CAE/CAM集成軟件,其技術領先,在機械、電子、航空、郵電、兵工、仿真等各行各業都有應用,在CAD/CAE/CAM領域中處于領先地位。它集零件設計、大型組件設計、鈑金設計、造型設計、模具開發、數控加工、運動分析、有限元分析、數據庫管理等功能于一身,具有參數化設計,特征驅動,單一數據庫等特點,大大加快了產品開發速度。本設計使用的Pro/Engineer Wildfire4.0是Pro/Engineer的新版本,其功能較以前的版本有了很大的提高,而且操作
15、界面也更為好用,可以大大提高技術人員的工作效率。1.6方案選擇本車設計采用單片膜片彈簧離合器。本車采用的摩擦式離合器是因為其結構簡單,可靠性強,維修方便,目前大多數汽車都采用這種形式的離合器。而采用干式離合器是因為濕式離合器大多是多盤式離合器,用于需要傳遞較大轉矩的離合器,而該車型不在此列。采用膜片彈簧離合器是因為膜片彈簧離合器具有很多優點:首先,由于膜片彈簧具有非線性特性,因此可設計成當摩擦片磨損后,彈簧壓力幾乎可以保持不變,且可減輕分離離合器時的踏板力,使操縱輕便;其次,膜片彈簧的安裝位置對離合器軸的中心線是對的,因此其壓力實際上不受離心力的影響,性能穩定,平衡性也好;再者,膜片彈簧本身兼
16、起壓緊彈簧和分離杠桿的作用,使離合器的結構大為簡化,零件數目減少,質量減小并顯著地縮短了其軸向尺寸;另外,由于膜片彈簧與壓盤是以整個圓周接觸,使壓力分布均勻,摩擦片的接觸良好,磨損均勻,也易于實現良好的散熱通風等。由于膜片彈簧離合器具有上述一系列的優點,并且制造膜片彈簧的工藝水平也在不斷地提高,因而這種離合器在轎車及微型、輕型客車上已得到廣泛的采用,而且逐漸擴展到載貨汽車上。從動盤選擇單片式從動盤是一位其結構簡單,調整方便。壓盤驅動方式采用傳動片式是因為其沒有太明顯的缺點且簡化了結構,降低了裝配要求又有利于壓盤定中。選擇拉式離合器是因為其較拉式離合器零件數目更少,結構更簡化,軸向尺寸更小,質量
17、更小;并且分離杠桿較大,使其踏板操縱力較輕。綜上本次設計選擇單片拉式膜片彈簧離合器。 4 從動盤總成設計4.1摩擦片設計離合器表面片在離合器接合過程中將遭到嚴重的滑磨,在相對很短的時間內產生大量的熱,因此,要求面片應有下列一些綜合性能:1、在工作時有相對較高的摩擦系數;2、在整個工作壽命期內應維持其摩擦特性,步希望出現,摩擦系數衰退現象;3、在短時間內能吸收相對高的能量,且有好的耐磨性能;4、能承受較高的壓盤作用載荷,在離合器接合過程中表現出良好的性能;5、能抵抗高轉速下大的離心力載荷而不破壞;6、在傳遞發動機轉矩時,有足夠的剪切強度;7、具有小的轉動慣量,材料加工性能良好;8、在整個正常工作
18、溫度范圍內,和對偶材料壓盤、飛輪等有良好的兼容摩擦性能;9、摩擦副對偶面有高度的溶污性能,不易影響它們的摩擦作用;10、具有良好的性能/價格比,不會污染環境。鑒于以上各點,近年來,摩擦材料的種類增長極快。挑選摩擦材料的基本原則是:1、滿足較高性能標準;2、成本最小;3、考慮代替石棉。本設計離合器摩擦片選用金屬陶瓷材料。它是由金屬機體、陶瓷成分和潤滑劑組成的一種多元復合材料。金屬基體的主要作用是以機體接合方式將陶瓷成分和潤滑劑保持其中,形成具有一定機械強度的整體;陶瓷組分主要起摩擦劑作用;而潤滑劑組分則主要起提高材料抗咬合性和抗戰粘性的潤滑作用,并使摩擦副工作平穩。潤滑劑組分和陶瓷組分一起共同形
19、成金屬陶瓷摩擦磨損性能調節劑。這種材料能和好的的完成上邊提到的各種要求,所以選擇這種材料。摩擦片的尺寸參數在第2.3節中已經查表得出,不再敘述。4.2從動盤轂設計從動盤毅的花鍵孔與變速器第一軸前端的花鍵軸以齒側定心矩形花鍵的動配合相聯接,以便從動盤毅能作軸向移動。花鍵的結構尺寸可根據從動盤外徑和發動機轉矩按GB1144-74選取(見表4.1)。從動盤毅花鍵孔鍵齒的有效長度約為花鍵外徑尺寸的(1.01. 4)倍(上限用于工作條件惡劣的離合器),以保證從動盤毅沿軸向移動時不產生偏斜。表4.1 GB1144-74從動盤外徑D/mm發動機轉矩/Nm花鍵齒數n花鍵外徑D/mm花鍵內徑d/mm鍵齒寬b/m
20、m有效齒長l/mm擠壓應力/MPa16050102318320101807010262132011.820011010292342511.322515010322643011.525020010352843510.428028010353244012.730031010403254010.732538010403254511.635048010403255013.238060010403255515.241072010453656013.143080010453656513.545095010524166512.5花鍵尺寸選定后應進行擠壓應力 ( MPa)及剪切應力j ( MPa)的強度校核:
21、 (4.1) (4.2)式中: ,分別為花鍵外徑及內徑,mm;n花鍵齒數;,b分別為花鍵的有效齒長及鍵齒寬,mm;z從動盤毅的數目;發動機最大轉矩,Nmm。從動盤毅通常由40Cr , 45號鋼、35號鋼鍛造,并經調質處理,HRC2832。由表4.1選取得:花鍵齒數n=10;花鍵外徑D=35mm;花鍵內徑D=28mm;鍵齒寬b=4mm;有效齒長l=35mm;擠壓應力=10.4MPa;校核=19.342MPa;=8.324MPa符合強度得要求。4.3從動片設計 從動片通常用1.32.0mm厚的鋼板沖壓而成。有時將其外緣的盤形部分磨薄至0.651.0mm,以減小其轉動慣量。從動片的材料與其結構型式有
22、關,整體式即不帶波形彈簧片的從動片,一般用高碳鋼(50或85號鋼)或65Mn鋼板,熱處理硬度HRC3848;采用波形彈簧片的分開式(或組合式)從動片,從動片采用08鋼板,氰化表面硬度HRC45,層深0.20.3mm;波形彈簧片采用65Mn鋼板,熱處理硬度 HRC4351。4.4扭轉減振器設計4.4.1扭轉減振器的功能為了降低汽車傳動系的振動,通常在傳動系中串聯一個彈性一阻尼裝置,它就是裝在離合器從動盤上的扭轉減振器。其彈性元件用來降低傳動系前端的扭轉剛度,降低傳動系扭振系統三節點振型的固有頻率,以便將較為嚴重的扭振車速移出常用車速范圍(當然,在實際中要做到這一點是非常困難的);其阻尼元件用來消
23、耗扭振能量,從而可有效地降低傳動系的共振載荷、非共振載荷及噪聲。4.4.2 扭轉減振器的結構類型的選擇圖4.1給出了幾種扭轉減振器的結構圖,它們之間的差異在于采用了不同的彈性元件和阻尼裝置。采用圓柱螺旋彈簧和摩擦元件的扭轉減振器(見圖4.1a-d)得到了最廣泛的應用。在這種結構中,從動片和從動盤毅上都開有6個窗口,在每個窗口中裝有一個減振彈簧,因而發動機轉矩由從動片傳給從動盤毅時必須通過沿從動片圓周切向布置的彈簧,這樣即將從動片和從動盤毅彈性地連接在一起,從而改變了傳動系統的剛度。當6個彈簧屬同一規格并同時起作用時,扭轉減振器的彈性特性為線性的。這種具有線性特性的扭轉減振器,結構較簡單,廣泛用
24、于汽油機汽車中。當6個彈簧屬于兩種或三種規格且剛度由小變大并按先后次序進人工作時,則稱為兩級或三級非線性扭轉減振器(圖4.1e為三級的)。這種非線性扭轉減振器,廣泛為現代汽車尤其是柴油發動機汽車所采用。柴油機的怠速旋轉不均勻度較大,常引起變速器常嚙合齒輪輪齒問的敲擊。為此,可使扭轉減振器具有兩級或三級非線性彈性特性。第一級剛度很小,稱怠速級,對降低變速器怠速噪聲效果顯著。線性扭轉減振器只能在一種載荷工況(通常為發動機最大轉矩)下有效地工作,而三級非線性扭轉減振器的彈性特性則擴大了適于其有效工作的載荷工況范圍,這有利于避免傳動系共振,降低汽車在行駛和怠速時傳動系的扭振和噪聲。 采用空心圓柱形見(
25、圖4.1f)或星形等其他形狀的橡膠彈性元件的扭轉減振器,也具有非線性的彈性特性。雖然其結構簡單、橡膠變形時具有較大的內摩擦,因而不需另加阻尼裝置,但由于它會使從動盤的轉動慣量顯著增大,且在離合器熱狀態下工作需用專門的橡膠制造,因此尚未得到廣泛采用。減振器的阻尼元件多采用摩擦片,在(圖4.1a)的結構中阻尼摩擦片的正壓力靠從1-從動片;2-從動盤轂;3-摩擦片;4-減振彈簧;5-碟形彈簧墊片;6-壓緊彈簧;7-減振盤;8-橡膠彈性元件圖4.1減振器結構圖動片與減振盤間的連接鉚釘建立。其結構雖簡單,但當摩擦片磨損后,阻尼力矩便減小甚至消失。為了保證正壓力從而阻尼力矩的穩定,可加進碟形彈簧(圖4.1
26、c,d),同時采用不同剛度的碟形彈簧和圓柱螺旋壓簧分別對兩組摩擦片建立不同的正壓力(圖4.1d),就可實現阻尼力矩的非線性變化。4.4.3扭轉減振器的參數確定1、扭轉減振器的角剛度減振器扭轉角剛度Ca決定于減振彈簧的線剛度及結構布置尺寸,按下列公式初選角剛度Ca13 (4.3)式中:為極限轉矩,按下式計算=(1.52.0) (4.4)式中:2.0適用乘用車,1.5適用商用車,本設計為商用車,選取1.5,為發動機最大扭矩,代入數值得=380,Ca 7273.5本設計初選Ca=7000N·m/raD。2、扭轉減振器最大摩擦力矩由于減振器扭轉剛度Ca受結構及發動機最大轉矩的限制,不可能很低
27、,故為了在發動機工作轉速范圍內最有效地消振,必須合理選擇減振器阻尼裝置的阻尼摩擦轉矩。一般可按下式初選為=(0.060.17) (4.5)取=0.15,本設計按其選取=28.5N·m。3、扭轉減振器的預緊力矩減振彈簧安裝時應有一定的預緊。這樣,在傳遞同樣大小的極限轉矩它將降低減振器的剛度,這是有利的,但預緊力值一般不應該大于摩擦力矩否則在反向工作時,扭轉減振器將停止工作。一般選取=(0.050.15)=19 N·m。4、扭轉減振器的彈簧分布半徑減振彈簧的分布尺寸R1的尺寸應盡可能大一些,一般取R1 =(0.600.75)D/2 (4.6)其中D為摩擦片內徑,代入數值,得R1
28、 =56mm。 5、扭轉減振器彈簧數目 可參考表4.1選取,本設計D=250mm,故選取Z=4。表4.2減振彈簧的選取離合器摩擦片外徑減振彈簧數目Z 225250 46 250325 68 325355 810 >350 10以上6、扭轉減振器減振彈簧的總壓力當限位彈簧與從動盤轂之間的間隙被消除時,彈簧傳遞扭矩達到最大Tj= (4.7)式中:的計算應按Tj的大者來進行=678.57N。每個彈簧工作壓力 (4.8)=169.64N。7、從動片相對從動盤轂的最大轉角 (4.9)=4.52 8、限位銷與從動盤缺口側邊的間隙 (4.10)式中:R2為限位銷的安裝半徑,一般為2.54mm。本設計取
29、=3。9、限位銷直徑限位銷直徑按結構布置選定,一般=9.512mm,本設計取=11。10、從動盤轂缺口寬度及安裝窗口尺寸為充分利用減振器的緩沖作用,將從動片上的部分窗口尺寸做的比從動盤轂上的窗口尺寸稍大一些,如圖4.2所示。 圖4.2 從動盤窗口尺寸簡圖一般推薦A1-A=a=1.416mm。這樣,當地面傳來沖擊時,開始只有部分彈簧參加工作,剛度較小,有利于緩和沖擊。本設計取a=1.5mm,A=25mm,A1=26.54.4.4減振彈簧的尺寸確定在初步選定減振器的主要尺寸后,即可根據布置上的可能來確定和減振彈簧設計的相關尺寸。彈簧的平均直徑:一般由結構布置決定,通常選取=1115左右。本設計選取=12。彈簧鋼絲直徑: (4.11)式中:扭轉許用應力=550600MPa
溫馨提示
- 1. 本站所有資源如無特殊說明,都需要本地電腦安裝OFFICE2007和PDF閱讀器。圖紙軟件為CAD,CAXA,PROE,UG,SolidWorks等.壓縮文件請下載最新的WinRAR軟件解壓。
- 2. 本站的文檔不包含任何第三方提供的附件圖紙等,如果需要附件,請聯系上傳者。文件的所有權益歸上傳用戶所有。
- 3. 本站RAR壓縮包中若帶圖紙,網頁內容里面會有圖紙預覽,若沒有圖紙預覽就沒有圖紙。
- 4. 未經權益所有人同意不得將文件中的內容挪作商業或盈利用途。
- 5. 人人文庫網僅提供信息存儲空間,僅對用戶上傳內容的表現方式做保護處理,對用戶上傳分享的文檔內容本身不做任何修改或編輯,并不能對任何下載內容負責。
- 6. 下載文件中如有侵權或不適當內容,請與我們聯系,我們立即糾正。
- 7. 本站不保證下載資源的準確性、安全性和完整性, 同時也不承擔用戶因使用這些下載資源對自己和他人造成任何形式的傷害或損失。
評論
0/150
提交評論